Lean Manufacturing ¿Qué es y cómo puede ayudarte?
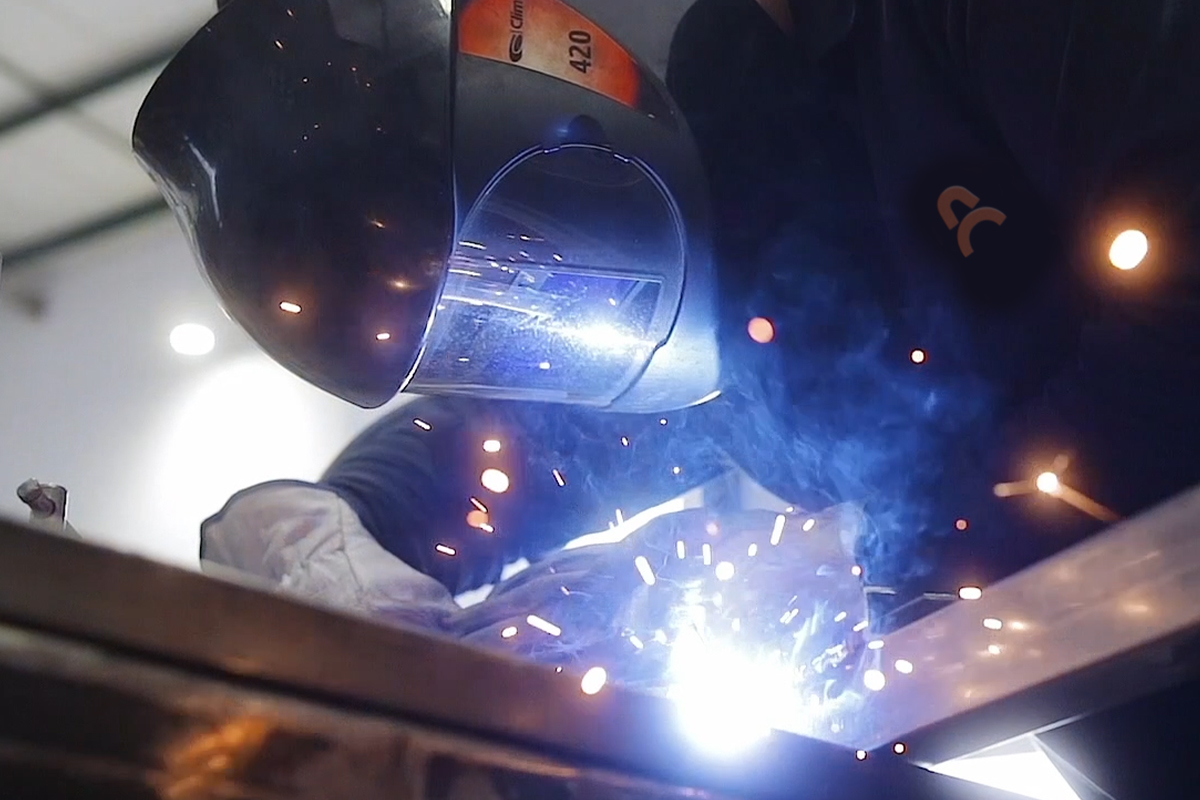
- Alsi
El Lean Manufacturing se conoce como un ‘modelo de gestión enfocado a la creación de flujo para poder entregar el máximo valor para los clientes, utilizando para ello los mínimos recursos necesarios’. Se le ocurrió a Toyota durante la década de 1950 en Japón, por eso originalmente fue conocido como el Sistema de Producción Toyota.
El objetivo de este modelo de gestión es mejorar y optimizar los sistemas de producción, eliminando toda actividad que no añada valor al mismo. De esta forma, gracias al Lean Manufacturing, puedes conseguir optimizar al máximo tus procesos y con ello, la rentabilidad de los mismos, en definitiva, se trata de una productividad inteligente que aumenta el valor agregado de los productos sin aumentar los costos de producción.
Factores
La metodología Lean Manufacturing trabaja en diferentes factores o niveles
1.Información y comunicación
A través de la planificación estratégica, reducimos esfuerzos innecesarios, evitando gastos no programados y reduciendo eventos imprevistos en los canales de distribución.
Por ejemplo, esa reunión tradicional que podría haberse resuelto con un email, es una manera de planificar estratégicamente el flujo de información.
2. Movimiento
Este factor se centra sobre todo en el movimiento de personas. Movilizar a diferentes empleados, interrumpir una actividad ya iniciada o hacer coincidir las agendas son ejemplos de situaciones que pueden producir pérdidas de energía y recursos.
3. Los tiempos
Se puede considerar que la espera es un problema para los trabajadores, así como la materia prima estacionaria. Por lo tanto, para que la administración se considere Lean, es necesario tener un flujo de trabajo continuo y bien definido. Los procesos inteligentes pueden ayudarte a reducir los tiempos de espera entre proceso y proceso.
4. Sobreproducción
Reducir el desperdicio es vital para reducir los costes innecesarios de una empresa. La sobreproducción puede generar productos terminados que no rotan y se acumulan.
La producción programada estratégicamente es uno de los factores principales de este modelo de organización que evita sobre costes.
5. Defectos
Llegamos al desperdicio causado por productos defectuosos. El re trabajo es una realidad que afecta en gran medida a las fábricas, por el desperdicio de materias primas.
Conocer los flujos y priorizar la calidad sobre la cantidad puede ser una forma de reducir este problema.
6. Procesamiento excesivo
En este punto hay que considerar todas las etapas de producción que no le agregan valor al producto final. Aquí es crucial la estandarización de procesos y criterios de calidad.
Cómo llevar a cabo una estrategia Lean Manufacturing
Estudio de métodos y tiempos
El primer paso para mejorar un proceso productivo es conocer todos los tiempos de fabricación y que estos tiempos sean totalmente reales.
Si no se conocen los tiempos de producción es imposible planificar y tampoco podemos calcular los costes de producción. Por tanto, antes de mejorar cualquier proceso de producción es necesario un estudio de tiempos, lo cual nos dará una visión general del proceso de producción, encontrando los procesos más lentos y en los cuales hay que prestar una mayor atención, ya que la mejora de estos procesos son los que más van a afectar a la producción total.
Con un correcto estudio de métodos y tiempos, se detectarán tiempos muertos al mismo tiempo que se eliminarán o reducirán los tiempos que no añadan valor al proceso y sus causas.
Planificación y seguimiento de la producción
Al conocer los tiempos reales de proceso se puede realizar una planificación de la producción, lo cual nos va a permitir corregir posibles imprevistos y adecuar los recursos necesarios para cumplir plazos de producción.
Teniendo la producción planificada, permite saber qué cantidad de materiales necesitas y lo más importante, cuándo los necesitas. Además, te permitirá tener los materiales a tiempo en cada proceso, lo que produce una reducción importante de tiempos muertos.
Una vez hecha la planificación, debes comprobar que se cumple tu estrategia de optimización, realizando un seguimiento continuo y exhaustivo de la producción y de los resultados.